5 Strong Hand Tools Every Welder Should Own
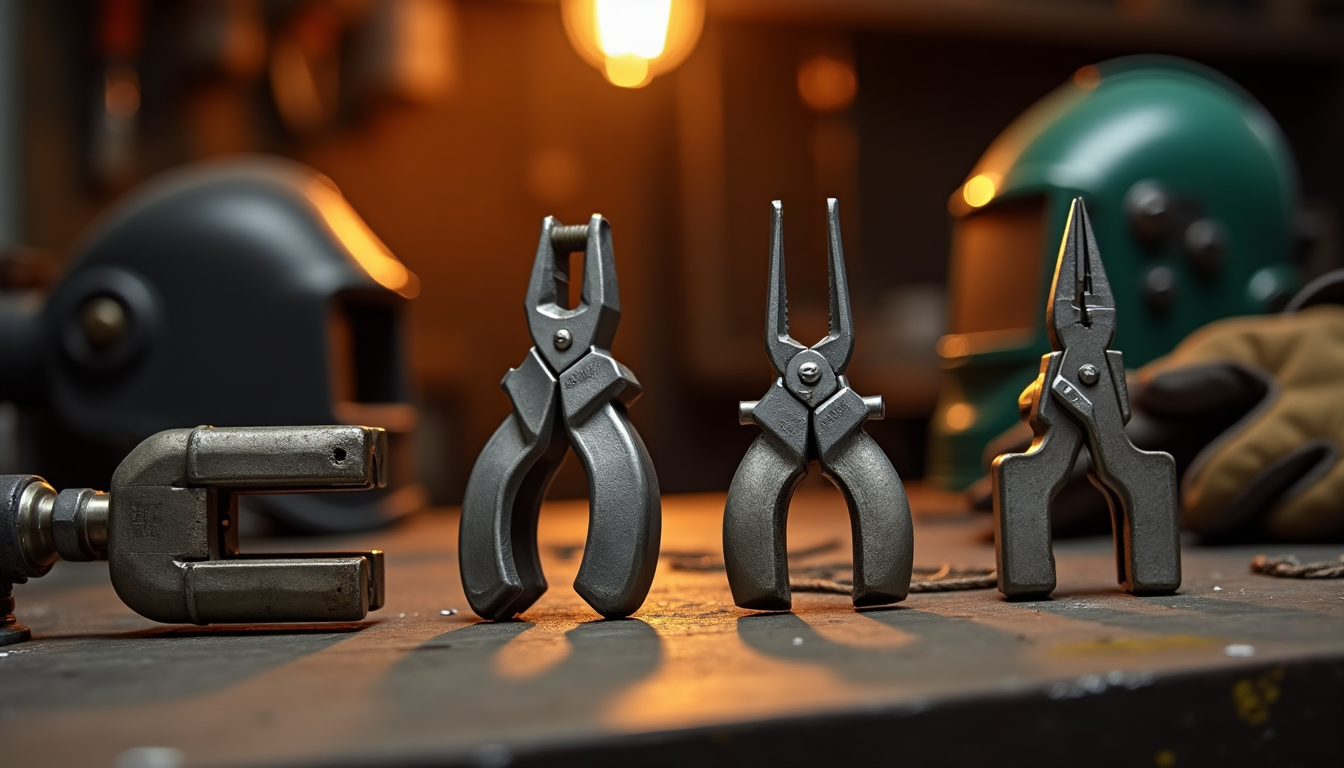
Welding requires precision and control, making strong hand tools essential for any professional or hobbyist welder. These tools play a crucial role in holding, positioning, and manipulating materials during the welding process. With the right set of hand tools, welders can improve their efficiency, accuracy, and overall quality of work.
This article explores five indispensable strong hand tools every welder should own. We’ll discuss welding clamps for secure fixturing, versatile pliers for various tasks, powerful welding magnets for positioning, specialized vises for holding workpieces, and other essential components for welding tables. By understanding the importance of these tools, welders can enhance their skills and produce better results in their metal fabrication projects.
Essential Welding Clamps
Welding clamps are indispensable tools for any welder, providing secure fixturing and precise positioning of workpieces. Among the various types available, quick-acting F-clamps, magnetic welding clamps, and C-clamps for heavy-duty use stand out as essential additions to a welder’s toolkit.
Quick-acting F-clamps
F-clamps, also known as bar clamps, have gained popularity among welders for their versatility and ease of use. These clamps feature an F-shaped frame with a sliding jaw that can be adjusted along the length of the bar. This design allows for a wide range of clamping capacities, making them suitable for various project sizes.
One notable advantage of F-clamps is their quick-acting mechanism. Many manufacturers, such as Strong Hand Tools, have re-engineered the traditional sliding arm clamp to improve efficiency. These redesigned F-clamps can be set up to 10 times faster than conventional C-clamps, significantly reducing preparation time for welding projects.
F-clamps are available in various sizes, with clamping capacities ranging from 8.5 inches to 12.5 inches or more. Some models, like the 4-in-1 clamps, offer enhanced versatility by incorporating multiple functions into a single tool. These clamps are typically constructed from high-quality, heat-treated steel and feature nickel/chrome plating for increased strength and durability.
Magnetic welding clamps
Magnetic welding clamps have revolutionized the way welders secure ferrous materials. These clamps utilize powerful electromagnetic or permanent magnet forces to hold workpieces in place, eliminating the need for mechanical clamping in many situations.
One of the primary advantages of magnetic clamps is their ability to securely hold metal workpieces without leaving marks or causing damage. This feature is particularly useful when working with finished surfaces or thin materials that may be prone to deformation under traditional clamping pressure.
Magnetic clamps come in various configurations, including fixed-angle and multi-angle options. Fixed-angle magnetic clamps, typically set at 90° or 135°, are ideal for welding corners or T-joints. Multi-angle magnetic clamps offer adjustable or pivoting magnets, accommodating a wide range of joint configurations and increasing versatility in welding applications.
These clamps are particularly beneficial in fabrication shops, construction sites, and shipyards, where they allow for quick positioning and repositioning of workpieces. This flexibility enhances productivity, especially when working with large or irregularly shaped components that may be challenging to secure with traditional clamps.
C-clamps for heavy-duty use
C-clamps remain a staple in welding workshops due to their robust construction and high clamping force capacity. These clamps consist of a C-shaped frame with a threaded screw mechanism that applies pressure to the workpiece.
Heavy-duty C-clamps are designed to handle thicker and heavier materials, making them ideal for structural steel welding and other demanding applications. These clamps often feature larger ACME threads and high-strength, drop-forged construction, allowing them to exert significant clamping force.
For instance, some heavy-duty C-clamps can generate up to 6,900 pounds of clamping force, ensuring that workpieces remain securely in place during welding operations. The clamping capacity of these tools can range from 4 inches to 12 inches or more, accommodating a wide variety of material thicknesses.
When selecting C-clamps for welding applications, it’s essential to consider factors such as throat depth, which determines how far the clamp can reach into the workpiece. Additionally, some models feature swivel pads that enable a strong grip without risking damage to the workpiece surface.
Must-Have Welding Pliers
Welding pliers are indispensable tools for any welder, offering versatility and efficiency in various welding tasks. These multi-functional tools have gained popularity among professionals and hobbyists alike due to their ability to handle multiple aspects of welding work.
Locking pliers
Locking pliers, also known as vise-grips, are essential for welding projects. These tools have a strong grip and can be locked in place, making them ideal for holding workpieces securely during welding. Strong Hand Tools offers a range of locking pliers designed specifically for welding applications. Their PR115 Locking C-Clamps, for instance, feature round tips and are constructed from nickel and chrome heat-treated steel, providing durability and strength.
For larger projects, the Strong Hand PR18S Locking C-Clamps offer a 10-inch throat depth, allowing welders to reach deeper into workpieces. These clamps come with swivel pads, ensuring a firm grip when clamping materials of various shapes and sizes.
Needle-nose pliers
Needle-nose pliers are crucial for precision work in welding. Their long, tapered jaws allow welders to reach into tight spaces and manipulate small components with ease. Many welding pliers incorporate needle-nose functionality, such as the YESWELDER 8″ MIG Welding Pliers, which feature a specially designed nose for efficient removal of welding spatter.
These pliers often come with additional features like wire cutters and serrated gripping surfaces. For example, some models include small serrated holes for installing and removing contact tips, as well as larger serrated holes for handling nozzles.
Multi-purpose welding pliers
Multi-purpose welding pliers combine several functions into one tool, making them a popular choice among welders. These pliers typically include features for cutting wires, removing and installing nozzles and contact tips, hammering, and cleaning spatter.
The JobSmart 8 in. Multi-Use MIG Welding Pliers exemplify this versatility. They feature a special jaw design for drawing out wire and removing or installing tips and nozzles. The carbon steel construction ensures durability, while the spring-loaded handle reduces hand fatigue during extended use.
Another example is the Strong Hand PG114, an 11″ multi-purpose welding plier that offers a range of functionalities in a single tool. These pliers are designed to handle various welding tasks efficiently, from manipulating workpieces to maintaining welding equipment.
When selecting welding pliers, consider factors such as comfort, durability, and specific features that align with your welding needs. High-quality pliers made from heat-treated steel or carbon steel offer longevity and reliable performance in demanding welding environments. By investing in a set of versatile welding pliers, welders can enhance their efficiency and tackle a wide range of tasks with greater ease and precision.
Versatile Welding Magnets
Welding magnets have become increasingly popular among welders due to their convenience and efficiency. These tools offer a hands-free approach to holding workpieces in place, allowing welders to focus on their craft without the need for complex fixtures or additional assistance.
On/off switchable magnets
One of the most useful innovations in welding magnets is the incorporation of on/off switches. These switchable magnets allow welders to control the magnetic force as needed, making positioning and removal of workpieces much easier. When the switch is in the “off” position, the magnet can be easily placed without attracting other tools or sticking to the workbench. Once the workpiece is in the desired position, the welder can simply flip the switch to “on,” activating the magnetic force and securing the material in place.
These switchable magnets typically offer holding forces of around 150 pounds, making them suitable for a wide range of welding applications. Some models, like the Adjust-O magnets, feature dual switches that provide even more control. With these, welders can lock one piece in place, align the second piece, and then secure it separately, ensuring precise positioning for tack welding.
Multi-angle welding magnets
Multi-angle welding magnets are versatile tools designed to hold workpieces at various angles, typically 45°, 90°, and 135°. These magnets are ideal for assembly, marking off, pipe installation, soldering, and welding tasks. Their ability to attract to any ferrous metal surface makes them highly adaptable for different project requirements.
Large switchable multi-angle welding magnets can offer holding forces of up to 24kg (55lbs) against 5mm thick mild steel. These powerful magnets provide a quick and easy way to hold two pieces of steel together while they are welded, soldered, or assembled. The mechanical switch feature allows for accurate positioning and easy cleaning, as any metal swarf can be wiped off when the magnet is turned off.
Magnetic V-pads
Magnetic V-pads are lightweight, low-profile tools that are particularly useful for small, light-duty, or intricate welding work. These clamps feature dual, pivoting magnetic heads that can position and hold angles up to 180°. Their versatility allows them to work on flat, angled, or round stock, making them invaluable for a variety of welding applications.
One of the key advantages of magnetic V-pads is their use of powerful rare earth magnets. Each pad typically contains four magnets, providing a strong hold on ferrous materials. This design makes them especially effective for holding round stock, which can be challenging with traditional clamps.
Magnetic V-pads come in various configurations to suit different needs. Some models feature magnets on the pad face only, while others have magnets on both the pad face and bottom for increased versatility. This flexibility allows welders to choose the most appropriate tool for their specific project requirements.
By incorporating these versatile welding magnets into their toolkit, welders can enhance their efficiency, improve precision, and tackle a wider range of projects with greater ease. The combination of switchable magnets, multi-angle capabilities, and specialized designs like V-pads provides welders with a comprehensive set of options for securing and positioning workpieces during the welding process.
Specialized Welding Vises
Specialized welding vises are essential tools for welders, providing stability and precision during various welding tasks. These vises offer unique features tailored to specific welding applications, enhancing efficiency and quality of work.
3-axis welding vise
The 3-axis welding vise is a versatile tool that allows welders to hold workpieces in multiple positions. This type of vise features quick-acting screws and a “swing away” arm, enabling welders to position parts in three dimensions before welding. The ability to hold workpieces in various angles makes it ideal for complex welding projects.
One notable feature of 3-axis welding vises is the quick-acting button, which allows the threaded screws to slide in and out for fast setup. This feature is particularly useful in fast-paced work environments where time is of the essence. Additionally, these vises often come with V-pads and magnetic rest blocks, which support and stabilize long stock during welding operations.
Pipe welding vise
Pipe welding vises are specifically designed to hold pipes securely during welding processes. These vises are made of durable, performance-proven materials and are engineered to resist strain, heat, and warping during tacking. The Ridgid 464 Flange Pipe Welding Vise, for example, has a pipe capacity of 2 1/2 in. to 8 in. and weighs 17 1/4 lb.
Pipe welding vises typically feature machined swivel nuts, pins, and special chain screws, which provide smooth and trouble-free assembly of the vise onto the pipe. This design allows welders to make position welds on straight runs with ease, helping them maintain proper fit during the welding process.
Angle welding vise
Angle welding vises are designed to hold workpieces at specific angles, typically 90 degrees, for precise welding of corners and joints. These vises are particularly useful for welding steel beams and other structural components that require right-angle connections.
The COGNATIVE W04C Ductile Iron Welding Machine Angle Clamp is an example of a heavy-duty angle welding vise. It’s well-constructed and capable of holding metal securely for welding tasks. Users have reported satisfaction with its build quality and functionality, noting its ability to clamp tightly and handle various materials, including 3/4″ diameter pipes.
When selecting a specialized welding vise, consider factors such as build material, build quality, and specific features that align with your welding needs. Ductile iron vises offer improved corrosion resistance and can handle heavier workloads compared to cast iron vises. For the absolute best in build material, forged iron vises provide superior strength, being approximately 26% stronger than ductile iron vises.
By incorporating these specialized welding vises into their toolkit, welders can enhance their precision, efficiency, and overall quality of work across a wide range of welding applications.
Conclusion
Equipping yourself with the right hand tools has a significant impact on your welding projects. From versatile clamps and pliers to powerful magnets and specialized vises, these tools enhance precision, efficiency, and overall quality of work. By investing in high-quality equipment, welders can tackle a wide range of tasks with greater ease and achieve better results.
As the welding industry continues to evolve, staying up-to-date with the latest tools and techniques is crucial to improve your skills. Whether you’re a seasoned professional or just starting out, having these essential hand tools in your arsenal will set you up for success. So, take some time to evaluate your toolkit and consider adding these game-changing tools to elevate your welding game.
FAQs
What hand tools are commonly used in welding?
In welding, some of the most frequently utilized hand tools include clamps, locking pliers, MIG welding pliers, chipping hammers, wire brushes, and various measuring tools.
What are the five essential parameters that influence welding?
The key parameters that govern welding are current, length of arc, angle, manipulation, and speed. The current affects the size and depth of the weld, while the length of the arc pertains to the distance between the work plates and the arc of a welding electrode.
What equipment is indispensable for every welder?
Every welder needs a variety of tools, with the most crucial being the welding machine. Other essential items include shielding gas and cylinders, consumable electrodes, a welding helmet, safety glasses, welding gloves, welding boots, and a welding jacket.
What are the five critical pieces of equipment for arc welding?
For arc welding, the essential equipment includes a welding machine, welding electrode, welding helmet, welding gloves, and safety glasses. The welding machine is used to generate the power needed to create the arc, and the welding electrode is used for melting metal to form the weld.
As a beginner in welding, what tools should I consider essential?
For anyone starting in welding, tools like clamps and vices are indispensable. These tools help in holding and securing materials during the welding process, making them crucial for effective and safe welding operations.